The Great Grinder War of 2009
-
- Boat Obsession Medal Finalist
- Posts: 684
- Joined: Wed Jan 25, 2006 6:28 pm
- Location: Beaufort, North Carolina
- Contact:
Re: The Great Grinder War of 2009
Day... Whatever.
I'm starting to suffer the monetary cash flow issues as bank balances dwindle, and sufferage charges... I mean, transfer charges accrue. I asked the owner of the boatyard today about my being here over 10 days... evidently I've been making enough headway that he's fine with me sticking around awhile.
Today was one of those days that just hurts. I bought two 2 inch seacocks, through hull fittings, and tail pieces. I also snagged a through hull for one of my original cockpit seacocks that is 1 1/4, and an adapter to bring the hose size to 1 1/2 inch for my sink drain. Four hundred and forty four dollars later... only had one seacock in stock, so the other will be here friday. (Anyone have a source for heavy gauge stainless sink drains? Mine is chromed steel, and rusted out. boooo.)
Also ordered another chainplate to match the schaffer on the otherside. I figure I'll use the layout of the boltholes if I decide to make an overkill set... but these will match the breaking strength of the wire I've got... soo...
I laid out the location for the new seacocks... laid a straight edge on top of a stack of 2x4's from the cockpit seats over the side of the boat. Measured down to the waterline, and down to the cockpit sole. Since the cockpit butts directly against the bulkhead, I'm going to move the front end of the cockpit back 7 inches, to give enough room to leave the tabbing un-marred. I'll probably go about replacing that bulkhead in the coming days... I've been wanting to adjust the cockpit area slightly, as when fully loaded with people the sole is to close to the waterline... and feet get wet.
I'm going to give above the waterline drains a try... well, more like slap in the middle of the boot stripe, as that is 4 inches of drop, plus 2 inches at her current weight.
After that I filled up my prop aperature fairing with acetone to dissolve out the foam, then cut it in half and gave it a looksie. Fits snug, ought to work about right. I've stalled on that one as I didn't think through a hollow bit below the waterline... may fill it with foam, or see about tracking down a load of lead shot polyester casting resin... well, she does need a touch of ballast aft right? grin!
I'm getting tired of running back and forth to Noel for tools that end up there part of the day, and on mine part of the day... i keep forgetting a set of drill bits so i can get started making backing plates for the seacocks. My jig saw will start a hole, but not in 3/4 inch marine grade... at least not without a lot of patience.
At some point today I planed the ash down to 1 inch thick stock for the compression posts, while the planer was running I ran a and power plane to take the excess epoxy off the mast beam. Finished up about the same time, planed down the beam and took over to the boat. At this point hunger struck, and I about broke the cardinal rule... Don't cut expensive pieces on your project while hungry and tired. My bevel gauge quit working so I found food. Came back with a refreshed brain and cut my version 2 mast beam to fit.
At some point today I went to the marine hardware store and picked up 30 bucks of 5/16ths 316 stainless bolts, fender washers,and cap nuts... Not the prettiest way to do it, but I like smooth shoulders on bolts in tightly fitting holes with bolts stretched. Shoulder bolts never wallow out, but more than that the slots don't strip out... Practical wins out again.
I goofed in my thinking for the compression posts i haven't made yet... as I have a 3 inch wide mast beam... plus the tabbing thickness, a 3 inch post would be narrower than the beam... derrr. So I've got a little more pondering to do in my pre-cut layout. It'll be close, as I'm on the border of having enough counting saw kerf... but I guess I know where the store is. grin.
Zach - Tired.
I'm starting to suffer the monetary cash flow issues as bank balances dwindle, and sufferage charges... I mean, transfer charges accrue. I asked the owner of the boatyard today about my being here over 10 days... evidently I've been making enough headway that he's fine with me sticking around awhile.
Today was one of those days that just hurts. I bought two 2 inch seacocks, through hull fittings, and tail pieces. I also snagged a through hull for one of my original cockpit seacocks that is 1 1/4, and an adapter to bring the hose size to 1 1/2 inch for my sink drain. Four hundred and forty four dollars later... only had one seacock in stock, so the other will be here friday. (Anyone have a source for heavy gauge stainless sink drains? Mine is chromed steel, and rusted out. boooo.)
Also ordered another chainplate to match the schaffer on the otherside. I figure I'll use the layout of the boltholes if I decide to make an overkill set... but these will match the breaking strength of the wire I've got... soo...
I laid out the location for the new seacocks... laid a straight edge on top of a stack of 2x4's from the cockpit seats over the side of the boat. Measured down to the waterline, and down to the cockpit sole. Since the cockpit butts directly against the bulkhead, I'm going to move the front end of the cockpit back 7 inches, to give enough room to leave the tabbing un-marred. I'll probably go about replacing that bulkhead in the coming days... I've been wanting to adjust the cockpit area slightly, as when fully loaded with people the sole is to close to the waterline... and feet get wet.
I'm going to give above the waterline drains a try... well, more like slap in the middle of the boot stripe, as that is 4 inches of drop, plus 2 inches at her current weight.
After that I filled up my prop aperature fairing with acetone to dissolve out the foam, then cut it in half and gave it a looksie. Fits snug, ought to work about right. I've stalled on that one as I didn't think through a hollow bit below the waterline... may fill it with foam, or see about tracking down a load of lead shot polyester casting resin... well, she does need a touch of ballast aft right? grin!
I'm getting tired of running back and forth to Noel for tools that end up there part of the day, and on mine part of the day... i keep forgetting a set of drill bits so i can get started making backing plates for the seacocks. My jig saw will start a hole, but not in 3/4 inch marine grade... at least not without a lot of patience.
At some point today I planed the ash down to 1 inch thick stock for the compression posts, while the planer was running I ran a and power plane to take the excess epoxy off the mast beam. Finished up about the same time, planed down the beam and took over to the boat. At this point hunger struck, and I about broke the cardinal rule... Don't cut expensive pieces on your project while hungry and tired. My bevel gauge quit working so I found food. Came back with a refreshed brain and cut my version 2 mast beam to fit.
At some point today I went to the marine hardware store and picked up 30 bucks of 5/16ths 316 stainless bolts, fender washers,and cap nuts... Not the prettiest way to do it, but I like smooth shoulders on bolts in tightly fitting holes with bolts stretched. Shoulder bolts never wallow out, but more than that the slots don't strip out... Practical wins out again.
I goofed in my thinking for the compression posts i haven't made yet... as I have a 3 inch wide mast beam... plus the tabbing thickness, a 3 inch post would be narrower than the beam... derrr. So I've got a little more pondering to do in my pre-cut layout. It'll be close, as I'm on the border of having enough counting saw kerf... but I guess I know where the store is. grin.
Zach - Tired.
1961 Pearson Triton
http://pylasteki.blogspot.com/
1942 Coast Guard Cutter - Rebuild
http://83footernoel.blogspot.com/
http://pylasteki.blogspot.com/
1942 Coast Guard Cutter - Rebuild
http://83footernoel.blogspot.com/
Re: The Great Grinder War of 2009
It's the Energizer Zach...:DZach wrote:Day... Whatever.
Glad to hear you're not going to be held to exactly ten days; it would be a shame to stop now, when you're on such a roll.
Now why didn't I think of that method, when I was debating moving my cockpit drain seacocks? Simple, quick, and clever.Zach wrote:I laid out the location for the new seacocks... laid a straight edge on top of a stack of 2x4's from the cockpit seats over the side of the boat. Measured down to the waterline, and down to the cockpit sole.
I can't quite visualize this part, but I'm curious about it.Zach wrote:Since the cockpit butts directly against the bulkhead, I'm going to move the front end of the cockpit back 7 inches, to give enough room to leave the tabbing un-marred.
Looking forward to your report on Day Whatever+1 :)
Rachel
-
- Boat Obsession Medal Finalist
- Posts: 684
- Joined: Wed Jan 25, 2006 6:28 pm
- Location: Beaufort, North Carolina
- Contact:
Re: The Great Grinder War of 2009
Today I had to make a supply run to lowes for drill bits and counter sinks, and another hack saw. (Hacksaws and 9/16ths box wrenches disappear...) Then to the bank (Ouch....) and swung by to pick up my other seacock.
With that done, it was a case of dodging raindrops and having to move inside. I cut out backing plates for the seacocks, and drilled out the hole for the sink to accommodate my 1 1/4 through hull.
After that, I spent some time dialing in exactly where I wanted the cockpit drains. I started yesterday by laying a straight edge across the cockpit seats and measuring down... establishing a horizontal plane of reference. I took a straight edge and lined it up against the aft end of the cabin top and marked the toe rail. Then hopped down to ground height, and picked up on the line vertically. laid a straight edge vertically in line with the forward end of the cockpit. Measuring back from that line I determined the location of the bulkhead inside... Then went from my mark at the toe rail, and measured diagonally to my chosen mark...
Switched sides, picked up the diagonal, and it was the same... Sweeeet.
I found out that the scribed line that shows the waterline is off port to starboard, and my painted boot stripe is a 1/2 inch different on each side... the holes however are symmetrical.
Then it was time to rip my lumber down to size for the compression posts. Gluing will be tomorrow, as I didn't have time to "make flat" on noel. Grin.
Zach
With that done, it was a case of dodging raindrops and having to move inside. I cut out backing plates for the seacocks, and drilled out the hole for the sink to accommodate my 1 1/4 through hull.
After that, I spent some time dialing in exactly where I wanted the cockpit drains. I started yesterday by laying a straight edge across the cockpit seats and measuring down... establishing a horizontal plane of reference. I took a straight edge and lined it up against the aft end of the cabin top and marked the toe rail. Then hopped down to ground height, and picked up on the line vertically. laid a straight edge vertically in line with the forward end of the cockpit. Measuring back from that line I determined the location of the bulkhead inside... Then went from my mark at the toe rail, and measured diagonally to my chosen mark...
Switched sides, picked up the diagonal, and it was the same... Sweeeet.
I found out that the scribed line that shows the waterline is off port to starboard, and my painted boot stripe is a 1/2 inch different on each side... the holes however are symmetrical.
Then it was time to rip my lumber down to size for the compression posts. Gluing will be tomorrow, as I didn't have time to "make flat" on noel. Grin.
Zach
1961 Pearson Triton
http://pylasteki.blogspot.com/
1942 Coast Guard Cutter - Rebuild
http://83footernoel.blogspot.com/
http://pylasteki.blogspot.com/
1942 Coast Guard Cutter - Rebuild
http://83footernoel.blogspot.com/
-
- Boat Obsession Medal Finalist
- Posts: 684
- Joined: Wed Jan 25, 2006 6:28 pm
- Location: Beaufort, North Carolina
- Contact:
Re: The Great Grinder War of 2009

Internet dropped out last night before I could get those up.
Dinnertime...
Zach
1961 Pearson Triton
http://pylasteki.blogspot.com/
1942 Coast Guard Cutter - Rebuild
http://83footernoel.blogspot.com/
http://pylasteki.blogspot.com/
1942 Coast Guard Cutter - Rebuild
http://83footernoel.blogspot.com/
-
- Candidate for Boat-Obsession Medal
- Posts: 320
- Joined: Thu Aug 16, 2007 6:54 pm
- Boat Name: Lady Kay IV
- Boat Type: 1990 Dragonfly 25
- Location: Bethlehem, PA
- Contact:
Re: The Great Grinder War of 2009
Bet they go the same place as utility knives, and, worst of all, measuring tapes. I have at least 5, probably 6 or 7 and sometimes I have them all in one pile, and then 24 hours later I can't find any......Hacksaws and 9/16ths box wrenches disappear...

Out there, alone, there is only truth.
-
- Boat Obsession Medal Finalist
- Posts: 684
- Joined: Wed Jan 25, 2006 6:28 pm
- Location: Beaufort, North Carolina
- Contact:
Re: The Great Grinder War of 2009
I bet! There has to be a pile of tools in another dimension....
Day 16
Today I laminated my compression posts... all 4 at one time. I did some figuring, and decided that it was doable. I used a reaaaal wide piece of polyetheylene sheeting, and wet out one post, wrapped it tight... wet out the next... till it was done. Took 16 ounces of resin to do it. Don't use an aluminum table as a sanding bench... you end up having to sand your work twice or forever hold your piece... with grey streaks!
Then I spent some time fitting my beam, after sanding off the last of the glue from the underside. Had to cut a relief on each side for the bulkhead tabbing... Ash is tough stuff, it laughed at my surform plane... and my rasp. Stuff that does that skips right to power tools for me, so I pulled out a hand power planer. Grin. I keep my Zach powered planes sharp enough to shave with, so rather not take them to all those glue lines. A few minutes going up and down the ladder, and it was nice and tight along the forward end, and plumb with the bulkhead. I decided when I laid out my jig to follow the contour of the cabintop parallel the bulkhead and smush the beam into thickened epoxy so there are no gaps... rather than set the bandsaw to the angle of the cabintop, and cut away beam. I'm figuring it'll be stronger with the beam intact.
With that done, I tried to buy some bronze flathead machine screws for my through hulls... the bummer about saturday, is that the shop that carries bronze isn't open. I may swing by West Marine and grab some tomorrow... (Ouchies $$!)
With the mast beam and compression posts at a plateau, I switched over and started adding glass to my through hull fittings. It's interesting that a hull 1 inch thick, takes almost 2 inches of glass to fill... back to the fair curve of the hull. I've got around 16 layers of biax in one of the old cockpit drains... and it's still not flush on the outside. (I taped the inside... grin!)
After dinner, I went at the cockpit bulkhead and cut out the starboard side tabbing. I used a cutoff wheel to cut the tabbing, then slid a long general purpose sawzall blade under it... and cut out all the purple lumps of filler that hold them in. I like the multimaster, but I wore out a 50 dollar blade doing the main bulkhead... Sawzall may not be faster, but it sure is more economical to wear out blades! The way you use a sawzall to cut something you don't care about away from something you do... is to get it started a little high in the scrap material, then turn the tool at an angle to the blade, about an 1/8th turn... When it works down to be parallel to the part you want to save, in this case the hull, you straighten it out and raise the angle of the tool to the hull so the blade works in a U shape... cutting all the way down flush on the tool side, and leaving the blade riding on the hull on the otherside. I have a lot of practice doing this... cutting out frames and old fasteners out of Noel, flush to the mahogany planks... (I had to stop 3 times and let the blade cool down... no sense working it till it loses its temper! When it does, you do too! Grin!)
It does a pretty decent job cutting off the leftover tabbing that pulls loose from the plywood... that likes to eat cut off wheels... Bend it into a U... 110 degrees or so with most of the blade flat to the hull, use the long ones. Keep the sawzall in the same spot and let the blade bend. They get hot real quick doing this, but hey... time is money.
Sawzalls continued... You can cut blind with them too, if you drag the tip across what you don't want to cut it'll vibrate and buck a bit... though you have to hold the tool greater than 45 degrees or so off the hull or it'll cut. Same deal if you want to cut a piece of wood nailed to another... start out about flat to it, then as it gets deeper into the cut stand it up let the tip dance on the wood behind it, and cut towards you. Time saving tip, as a sawzall is a delicate instrument, if you know how it can't cut something.... Grin. A lot of times you'll do better flipping the blade upside down to get better clearance. I use a mini sawzall from Northern Tool and equipment, even though there is a Milwaukee laying around. The less space from the blade to the body, the tighter a cut you can make!
After that, I started on the port side clearing out access to the cockpit bulkhead. Both sides the tabbing had separated at the top, and was a bit rotten... may as well keep at it!
Zach - Hopefully be back in the water late next week, I'm deciding how much I can do/want to do at 15 bucks a day... working on the hard vs in the water has such a huge speed benefit. I may give a go at getting the decks painted. I was less than pleased grinding back into the area I recored re-using the old skin... may take that back down to the balsa if I do. Pretty much trying to hammer out the big stuff that I can't do in the water or with the mast stepped.
Day 16
Today I laminated my compression posts... all 4 at one time. I did some figuring, and decided that it was doable. I used a reaaaal wide piece of polyetheylene sheeting, and wet out one post, wrapped it tight... wet out the next... till it was done. Took 16 ounces of resin to do it. Don't use an aluminum table as a sanding bench... you end up having to sand your work twice or forever hold your piece... with grey streaks!
Then I spent some time fitting my beam, after sanding off the last of the glue from the underside. Had to cut a relief on each side for the bulkhead tabbing... Ash is tough stuff, it laughed at my surform plane... and my rasp. Stuff that does that skips right to power tools for me, so I pulled out a hand power planer. Grin. I keep my Zach powered planes sharp enough to shave with, so rather not take them to all those glue lines. A few minutes going up and down the ladder, and it was nice and tight along the forward end, and plumb with the bulkhead. I decided when I laid out my jig to follow the contour of the cabintop parallel the bulkhead and smush the beam into thickened epoxy so there are no gaps... rather than set the bandsaw to the angle of the cabintop, and cut away beam. I'm figuring it'll be stronger with the beam intact.
With that done, I tried to buy some bronze flathead machine screws for my through hulls... the bummer about saturday, is that the shop that carries bronze isn't open. I may swing by West Marine and grab some tomorrow... (Ouchies $$!)
With the mast beam and compression posts at a plateau, I switched over and started adding glass to my through hull fittings. It's interesting that a hull 1 inch thick, takes almost 2 inches of glass to fill... back to the fair curve of the hull. I've got around 16 layers of biax in one of the old cockpit drains... and it's still not flush on the outside. (I taped the inside... grin!)
After dinner, I went at the cockpit bulkhead and cut out the starboard side tabbing. I used a cutoff wheel to cut the tabbing, then slid a long general purpose sawzall blade under it... and cut out all the purple lumps of filler that hold them in. I like the multimaster, but I wore out a 50 dollar blade doing the main bulkhead... Sawzall may not be faster, but it sure is more economical to wear out blades! The way you use a sawzall to cut something you don't care about away from something you do... is to get it started a little high in the scrap material, then turn the tool at an angle to the blade, about an 1/8th turn... When it works down to be parallel to the part you want to save, in this case the hull, you straighten it out and raise the angle of the tool to the hull so the blade works in a U shape... cutting all the way down flush on the tool side, and leaving the blade riding on the hull on the otherside. I have a lot of practice doing this... cutting out frames and old fasteners out of Noel, flush to the mahogany planks... (I had to stop 3 times and let the blade cool down... no sense working it till it loses its temper! When it does, you do too! Grin!)
It does a pretty decent job cutting off the leftover tabbing that pulls loose from the plywood... that likes to eat cut off wheels... Bend it into a U... 110 degrees or so with most of the blade flat to the hull, use the long ones. Keep the sawzall in the same spot and let the blade bend. They get hot real quick doing this, but hey... time is money.
Sawzalls continued... You can cut blind with them too, if you drag the tip across what you don't want to cut it'll vibrate and buck a bit... though you have to hold the tool greater than 45 degrees or so off the hull or it'll cut. Same deal if you want to cut a piece of wood nailed to another... start out about flat to it, then as it gets deeper into the cut stand it up let the tip dance on the wood behind it, and cut towards you. Time saving tip, as a sawzall is a delicate instrument, if you know how it can't cut something.... Grin. A lot of times you'll do better flipping the blade upside down to get better clearance. I use a mini sawzall from Northern Tool and equipment, even though there is a Milwaukee laying around. The less space from the blade to the body, the tighter a cut you can make!
After that, I started on the port side clearing out access to the cockpit bulkhead. Both sides the tabbing had separated at the top, and was a bit rotten... may as well keep at it!
Zach - Hopefully be back in the water late next week, I'm deciding how much I can do/want to do at 15 bucks a day... working on the hard vs in the water has such a huge speed benefit. I may give a go at getting the decks painted. I was less than pleased grinding back into the area I recored re-using the old skin... may take that back down to the balsa if I do. Pretty much trying to hammer out the big stuff that I can't do in the water or with the mast stepped.
1961 Pearson Triton
http://pylasteki.blogspot.com/
1942 Coast Guard Cutter - Rebuild
http://83footernoel.blogspot.com/
http://pylasteki.blogspot.com/
1942 Coast Guard Cutter - Rebuild
http://83footernoel.blogspot.com/
Re: The Great Grinder War of 2009
He just keeps going, and going, and... :D
$15 per day sounds awfully reasonable, and you're there. Might as well keep going if you can, seems like.
What didn't you like when you were grinding on the re-used deck skin?
Rachel
$15 per day sounds awfully reasonable, and you're there. Might as well keep going if you can, seems like.
What didn't you like when you were grinding on the re-used deck skin?
Rachel
-
- Boat Obsession Medal Finalist
- Posts: 684
- Joined: Wed Jan 25, 2006 6:28 pm
- Location: Beaufort, North Carolina
- Contact:
Re: The Great Grinder War of 2009
Re-used skin: Lots of voids in the goo... not the super solid bond I was thinking.
Day 17
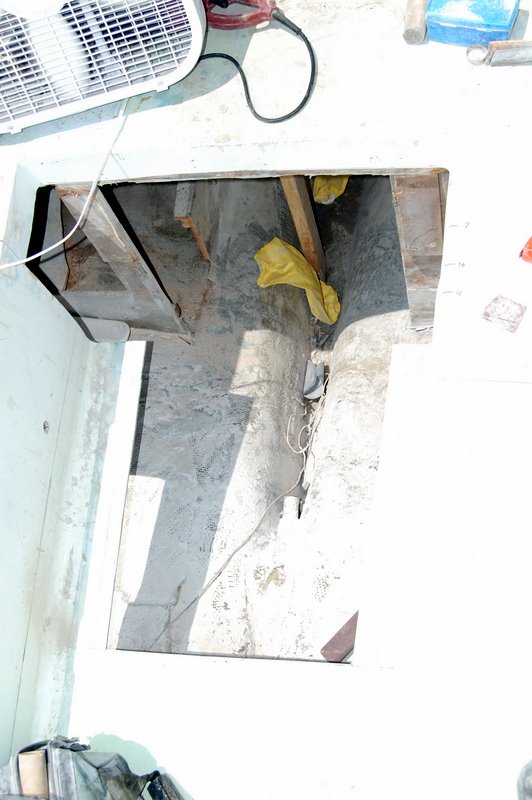
Today I ground down my through hull patches again... This seems to be a generic way to start the day. I'm impressed with how much glass it takes to fill a boat this thick! Still have a ways to go on two of them. I'm using a really flexible batten to follow the curve of the hull, that and my semi-tuned finger tips for the vertical curvy'ness.
With that done I marked my lines on the cockpit sole and sides... and cut out the sole forward the plywood support, and leaving some meat around the top so it would hold its shape. Tritons are beasts... I can step on the edge of the sole I left (4-5 inches wide depending on the location of the reinforcement...) and it hardly deflects. I think if they'd run the reinforcements side to side instead of fore and aft, it wouldn't bow and squeak!
Anyway, took about 2 minutes to cut it out... and about 5 to just look at it and visualize where the lower water pump bolt... distributor clamp... and transmission clutch adjusting bolt... used to be. By golly, with a lift up lid right there, I might keep an inboard in a triton. Idea noted...
With that done I cut out the starboard cockpit bulkhead, and ground down the tabbing. It had 3 layers of roving... and mat. By golly, that made a lot of dust!
I then went to town cutting out the cockpit locker lid drains. These things have a crazy amount of drop to them, I'm thinking Pearson intended them to be stiffeners... but if you've ever tried to pull a fender out of a locker, or worse... shimmied inside one to take something loose from the deck... they are some kind of in the way. I do believe they'd probably still drain downward with the lid underwater though...
After that I measured down from the deck at intervals, sort of the reverse of lofting a boat... and made a template for my plywood bulkheads that will run along side the cockpit. I then cut out the wooden reinforcement on the port side, that kept the cutout for the locker lid from bowing in and out. I'm bringing the plywood up almost to the edge, as I want the thing never to squeak again when I step on it. The cockpit is the one place on a triton, besides the chainplates... that doesn't scream absolute, absurd overkill... so it must be brought inline with the rest of the boat. Grin.
With that done, I cut out a template for the starboard cockpit bulkhead... and seramoniously tossed the old skinny one overboard.
I'm going to install my seacocks officially when I've glassed in everything. Stupid... yes. I just know I'll need an access hatch somewhere, in order to put on a hose clamp or something dumb... and the only way I know how to get it right the first time, is to install it when the rest is already there. I call it the heater core theory. Cars, they start with a heater core as the blank slate... then they put a firewall on oneside, with a hole slightly smaller than the core... then they install a dashboard to its backside... Fastest way to replace one, is to buy a new heater core and build a car around it... Nothing on this boat will be like that if I can help it!
I then got started sawzalling out the starboard side cockpit locker lid drains... and had a guy wander out of his boat around 9:30... guess he was spending the night aboard... So I quieted it down and packed up for the evening.
Zach - clogged up another set of pre-filters, and wondered why the world started spinning... Obituary reads - "Suffocated by respirator."
Pictures on blog...
Day 17
Today I ground down my through hull patches again... This seems to be a generic way to start the day. I'm impressed with how much glass it takes to fill a boat this thick! Still have a ways to go on two of them. I'm using a really flexible batten to follow the curve of the hull, that and my semi-tuned finger tips for the vertical curvy'ness.
With that done I marked my lines on the cockpit sole and sides... and cut out the sole forward the plywood support, and leaving some meat around the top so it would hold its shape. Tritons are beasts... I can step on the edge of the sole I left (4-5 inches wide depending on the location of the reinforcement...) and it hardly deflects. I think if they'd run the reinforcements side to side instead of fore and aft, it wouldn't bow and squeak!
Anyway, took about 2 minutes to cut it out... and about 5 to just look at it and visualize where the lower water pump bolt... distributor clamp... and transmission clutch adjusting bolt... used to be. By golly, with a lift up lid right there, I might keep an inboard in a triton. Idea noted...
With that done I cut out the starboard cockpit bulkhead, and ground down the tabbing. It had 3 layers of roving... and mat. By golly, that made a lot of dust!
I then went to town cutting out the cockpit locker lid drains. These things have a crazy amount of drop to them, I'm thinking Pearson intended them to be stiffeners... but if you've ever tried to pull a fender out of a locker, or worse... shimmied inside one to take something loose from the deck... they are some kind of in the way. I do believe they'd probably still drain downward with the lid underwater though...
After that I measured down from the deck at intervals, sort of the reverse of lofting a boat... and made a template for my plywood bulkheads that will run along side the cockpit. I then cut out the wooden reinforcement on the port side, that kept the cutout for the locker lid from bowing in and out. I'm bringing the plywood up almost to the edge, as I want the thing never to squeak again when I step on it. The cockpit is the one place on a triton, besides the chainplates... that doesn't scream absolute, absurd overkill... so it must be brought inline with the rest of the boat. Grin.
With that done, I cut out a template for the starboard cockpit bulkhead... and seramoniously tossed the old skinny one overboard.
I'm going to install my seacocks officially when I've glassed in everything. Stupid... yes. I just know I'll need an access hatch somewhere, in order to put on a hose clamp or something dumb... and the only way I know how to get it right the first time, is to install it when the rest is already there. I call it the heater core theory. Cars, they start with a heater core as the blank slate... then they put a firewall on oneside, with a hole slightly smaller than the core... then they install a dashboard to its backside... Fastest way to replace one, is to buy a new heater core and build a car around it... Nothing on this boat will be like that if I can help it!
I then got started sawzalling out the starboard side cockpit locker lid drains... and had a guy wander out of his boat around 9:30... guess he was spending the night aboard... So I quieted it down and packed up for the evening.
Zach - clogged up another set of pre-filters, and wondered why the world started spinning... Obituary reads - "Suffocated by respirator."
Pictures on blog...
1961 Pearson Triton
http://pylasteki.blogspot.com/
1942 Coast Guard Cutter - Rebuild
http://83footernoel.blogspot.com/
http://pylasteki.blogspot.com/
1942 Coast Guard Cutter - Rebuild
http://83footernoel.blogspot.com/
-
- Boat Obsession Medal Finalist
- Posts: 684
- Joined: Wed Jan 25, 2006 6:28 pm
- Location: Beaufort, North Carolina
- Contact:
Re: The Great Grinder War of 2009
Day 18
Today i had to spend the morning on Noel doing some work with the rubrails...
After that I went to town cutting tabbing for the new plywood going in under the cockpit. Lots and lots of glass...
Then the wind picked up... and the sky turned dark... and I decided that maybe the weather guy would be right for once and we might get thunderstorms. I covered the boat in tarps. It was actually kind of nice to have a lot of wind rather than a little... as once I had one side tied down at each corner the tarp blew against the boat so hard it stayed in one spot...
After that I finished grinding out the leftover remnants of the cockpit lid drains, and the clumps of mat and barney filler that held on the wood reinforcement. My hands are starting to complain about all the grinding...
I cut out the plywood wedge that will line the side of the cockpit, fit like a glove on the port side. Starboard side, the aft most min-bulkhead in the boat is askew... so I'm modifying the length of both to build towards symmetry and rather than what is there. (little things bug me...)
I've got the image of an Alerion 28's stern deck burned in my mind after stepping on board one at last years Annapolis boat show. If I paint the deck while she's out, I'll reconfigure the stern deck to something similar.
i finished test fitting my bulkhead, which fit entirely to tight the first time out... No light visible through the gap through 2/3rds of it. It popped in place, literally... and I had to work to get it back out. Hmm... I again over worked and started shaving and test fitting planing down till perfection (OCD kicked in...) and kicked myself when I realized I'm going to float these bulkheads on foam too. Duh.
My bolt came in for the mast tabernacle. 1 inch diameter, 316 stainless... 6 inch shoulder. $$$
I spotted a 1 inch stainless lock nut on the shelf of one of the marine hardware stores today... MINE!
As of now, the rain hasn't come... but I'm gonna keep her tarped until I get the cockpit back water tight.
Today i had to spend the morning on Noel doing some work with the rubrails...
After that I went to town cutting tabbing for the new plywood going in under the cockpit. Lots and lots of glass...
Then the wind picked up... and the sky turned dark... and I decided that maybe the weather guy would be right for once and we might get thunderstorms. I covered the boat in tarps. It was actually kind of nice to have a lot of wind rather than a little... as once I had one side tied down at each corner the tarp blew against the boat so hard it stayed in one spot...
After that I finished grinding out the leftover remnants of the cockpit lid drains, and the clumps of mat and barney filler that held on the wood reinforcement. My hands are starting to complain about all the grinding...
I cut out the plywood wedge that will line the side of the cockpit, fit like a glove on the port side. Starboard side, the aft most min-bulkhead in the boat is askew... so I'm modifying the length of both to build towards symmetry and rather than what is there. (little things bug me...)
I've got the image of an Alerion 28's stern deck burned in my mind after stepping on board one at last years Annapolis boat show. If I paint the deck while she's out, I'll reconfigure the stern deck to something similar.
i finished test fitting my bulkhead, which fit entirely to tight the first time out... No light visible through the gap through 2/3rds of it. It popped in place, literally... and I had to work to get it back out. Hmm... I again over worked and started shaving and test fitting planing down till perfection (OCD kicked in...) and kicked myself when I realized I'm going to float these bulkheads on foam too. Duh.
My bolt came in for the mast tabernacle. 1 inch diameter, 316 stainless... 6 inch shoulder. $$$
I spotted a 1 inch stainless lock nut on the shelf of one of the marine hardware stores today... MINE!
As of now, the rain hasn't come... but I'm gonna keep her tarped until I get the cockpit back water tight.
1961 Pearson Triton
http://pylasteki.blogspot.com/
1942 Coast Guard Cutter - Rebuild
http://83footernoel.blogspot.com/
http://pylasteki.blogspot.com/
1942 Coast Guard Cutter - Rebuild
http://83footernoel.blogspot.com/
-
- Candidate for Boat-Obsession Medal
- Posts: 320
- Joined: Thu Aug 16, 2007 6:54 pm
- Boat Name: Lady Kay IV
- Boat Type: 1990 Dragonfly 25
- Location: Bethlehem, PA
- Contact:
Re: The Great Grinder War of 2009
You mean the buzzing and the cramping.....? I hate that.My hands are starting to complain about all the grinding...
Out there, alone, there is only truth.
-
- Boat Obsession Medal Finalist
- Posts: 684
- Joined: Wed Jan 25, 2006 6:28 pm
- Location: Beaufort, North Carolina
- Contact:
Re: The Great Grinder War of 2009
I don't get the buzzing, but they lock up over night and are pretty much useless in the morning... that and my one handed, reaching around the corner with the grinder has slowed down a bit...
Today I helped install new prop shafts on Noel, and they were in around noon.
My box fan blew up. Well, went out in a whimper... Last month it took a swim over the side in salt water, so it was on borrowed time anyway.
Today I cut out the plywood for the cockpit lockers, and fit them in place. I removed the starboard side of the beam that runs under the bridge deck, and fit the plywood bulkhead flush to the edge of the cockpit, as the way it was done warped the panel in place... not flat.
I ground out random bits of tabbing, and cleaned up the resinous goop, the same orangey stuff that grinds into fluff balls that lined the bilge. With all that out of the way, I cut out the cockpit support in front of the rudder tube... cockpit sagged an 1/8th inch. (I love this boat... ) Then I cut the cockpit sole out leaving a 3 1/2 inches around the rudder tube.
Then I spent forever, hand sanding the contours of the rudder tube to get the orange goop off, and fiberglassed late into the night. Slow going, as my roller died tonight. It will turn by hand, but does not turn when rolled on the fabric. Had to go back to using a squeedgee... Made it 2 years and a whole lot of abuse...
Tomorrow: Finish beefing up the rudder tube, glass in cockpit plywood....
I'm really struggling not to build a wooden boat cockpit back into her, it'd be a piece of cake to screw two battens to each sheet of plywood and lay another on top as the sole... then glass everything in place... "I will not build a wooden boat... I will not build a wooden boat... out of a plastic one."
Zach
Today I helped install new prop shafts on Noel, and they were in around noon.
My box fan blew up. Well, went out in a whimper... Last month it took a swim over the side in salt water, so it was on borrowed time anyway.
Today I cut out the plywood for the cockpit lockers, and fit them in place. I removed the starboard side of the beam that runs under the bridge deck, and fit the plywood bulkhead flush to the edge of the cockpit, as the way it was done warped the panel in place... not flat.
I ground out random bits of tabbing, and cleaned up the resinous goop, the same orangey stuff that grinds into fluff balls that lined the bilge. With all that out of the way, I cut out the cockpit support in front of the rudder tube... cockpit sagged an 1/8th inch. (I love this boat... ) Then I cut the cockpit sole out leaving a 3 1/2 inches around the rudder tube.
Then I spent forever, hand sanding the contours of the rudder tube to get the orange goop off, and fiberglassed late into the night. Slow going, as my roller died tonight. It will turn by hand, but does not turn when rolled on the fabric. Had to go back to using a squeedgee... Made it 2 years and a whole lot of abuse...
Tomorrow: Finish beefing up the rudder tube, glass in cockpit plywood....
I'm really struggling not to build a wooden boat cockpit back into her, it'd be a piece of cake to screw two battens to each sheet of plywood and lay another on top as the sole... then glass everything in place... "I will not build a wooden boat... I will not build a wooden boat... out of a plastic one."
Zach
1961 Pearson Triton
http://pylasteki.blogspot.com/
1942 Coast Guard Cutter - Rebuild
http://83footernoel.blogspot.com/
http://pylasteki.blogspot.com/
1942 Coast Guard Cutter - Rebuild
http://83footernoel.blogspot.com/
- Tim
- Shipwright Extraordinaire
- Posts: 5708
- Joined: Tue Apr 01, 2003 6:39 pm
- Boat Name: Glissando
- Boat Type: Pearson Triton
- Location: Whitefield, ME
- Contact:
Re: The Great Grinder War of 2009
You haven't made it clear what this latest round of cockpit destruction is attempting to accomplish. Enlighten us..why are you cutting everything out?
Also, where are the pictures from the past couple days? Not acceptable.
Also, where are the pictures from the past couple days? Not acceptable.
---------------------------------------------------
Forum Founder--No Longer Participating
Forum Founder--No Longer Participating
-
- Candidate for Boat-Obsession Medal
- Posts: 320
- Joined: Thu Aug 16, 2007 6:54 pm
- Boat Name: Lady Kay IV
- Boat Type: 1990 Dragonfly 25
- Location: Bethlehem, PA
- Contact:
Re: The Great Grinder War of 2009
Because he has a grinder?why are you cutting everything out?

Out there, alone, there is only truth.
Re: The Great Grinder War of 2009
I remember you explaining it earlier, but I couldn't visualize what you meant. Then I saw you cutting interesting shapes out of the cockpit. Now I, too, am itching to know just what's going on :D
Yes... photo-less blog posts. They have been noticed. Surely you can make time at the end of a 12-hour day to include a few ;)
Rachel
Yes... photo-less blog posts. They have been noticed. Surely you can make time at the end of a 12-hour day to include a few ;)
Rachel
-
- Boat Obsession Medal Finalist
- Posts: 684
- Joined: Wed Jan 25, 2006 6:28 pm
- Location: Beaufort, North Carolina
- Contact:
Re: The Great Grinder War of 2009
Grin...
The plan is to make the cockpit lockers water tight, hence moving the cockpit drains through each locker where a leak won't sink the boat...
Why cut out the cockpit sole? So I can tab in two plywood bulkheads running longways between the lazarette, and the bulkhead that divides the cabin from the cockpit lockers... Which I'm replacing with solid pieces of plywood.
I'm 6 feet one inch tall, and 190 lbs.. 37 inch long arms. I'm about like a T-Rex working in tight places, all fore arms... So if its a flat piece of glass that can easily be put back in place, it's easier to cut out whats needed to make access... Plus I'm building a curved sole on a piece of smoooth tile board to put an arch in a prefab sole.
Hope that explains the why's and hows.
Taking the night off, unless I get a second wind... cut out 20 feet of plywood and fiberglass off Noel today, redoing the sheathing on the hull below the rub rail.
Zach
Todays work:

Last nights hand sanding:
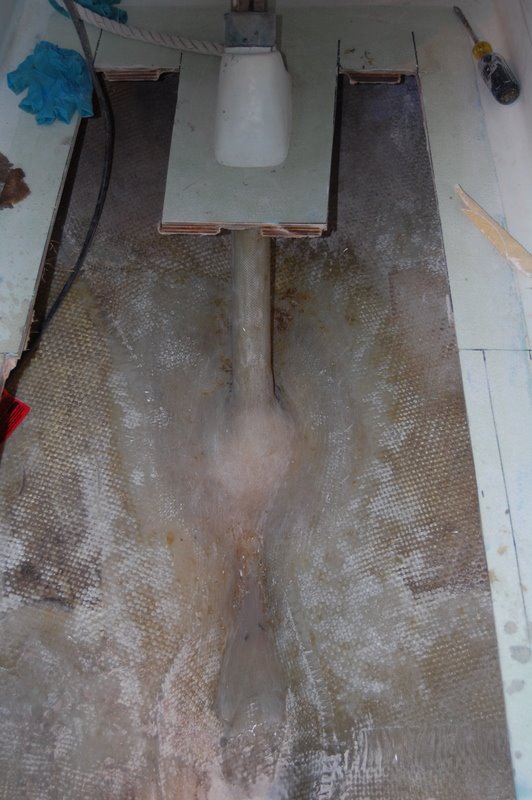
The plan is to make the cockpit lockers water tight, hence moving the cockpit drains through each locker where a leak won't sink the boat...
Why cut out the cockpit sole? So I can tab in two plywood bulkheads running longways between the lazarette, and the bulkhead that divides the cabin from the cockpit lockers... Which I'm replacing with solid pieces of plywood.
I'm 6 feet one inch tall, and 190 lbs.. 37 inch long arms. I'm about like a T-Rex working in tight places, all fore arms... So if its a flat piece of glass that can easily be put back in place, it's easier to cut out whats needed to make access... Plus I'm building a curved sole on a piece of smoooth tile board to put an arch in a prefab sole.
Hope that explains the why's and hows.
Taking the night off, unless I get a second wind... cut out 20 feet of plywood and fiberglass off Noel today, redoing the sheathing on the hull below the rub rail.
Zach
Todays work:

Last nights hand sanding:
1961 Pearson Triton
http://pylasteki.blogspot.com/
1942 Coast Guard Cutter - Rebuild
http://83footernoel.blogspot.com/
http://pylasteki.blogspot.com/
1942 Coast Guard Cutter - Rebuild
http://83footernoel.blogspot.com/
-
- Boat Obsession Medal Finalist
- Posts: 684
- Joined: Wed Jan 25, 2006 6:28 pm
- Location: Beaufort, North Carolina
- Contact:
Re: The Great Grinder War of 2009
Today was cut the bulwarks off the stern of Noel day... Sawzalls, angle grinders, and really big hammers... Oh my! (Glassing the deck, over the rub rail, and down to the new sheathing...)
Mid-afternoon I took off, and snagged my mast from the boat yard. Brought it back to the shop, and my friend Brian and I stripped the hardware off the lower foot or so. Then he made a set of doublers, 3 and something inches in diameter to weld around an aluminum compression tube. While he did that I bored the holes in my massive pieces of aluminum angle, to take the 1 inch 316 stainless bolt... With that done, we found the center on each side of the extrusion (Thankfully mine has a flat spot where the main sail track goes...) and bored he bored the holes. My mast is slap full of foam.
Anyone have ideas on fishing a new masthead wire in to a solid block of foam?
Anyway, after that I took a huge hose clamp and wrapped it around the mast... marked it with a sharpie... and I cut off the lower few inches that held the end plate that indexes into the mast step firmly in place. 48 years of stainless screws through aluminum into cast aluminum... ain't coming out. I'll have to fish mouth the end of the mast anyway, so that it will clear the deck as it swings its arc. Yes, this is one of those moments in time where one things to themselves... no do-overs!
With that done, it was 4:00... quitting time at the yard, so I took off to the other where Pylasteki resides.
I've decided to do all I can think of inside the cockpit lockers before buttoning them up, today that meant wire brushing the paint off the starboard locker. Whatever it was Pearson used, was some rediculously good paint to still be around 48 years later... at least on my boat it has a pretty tenacious hold, to bad it is hideous speckled stuff in an off-beige brown. I'm going back with a semi-gloss white acrylic enamel (Rustoleum... grin) as I want something smooth enough to be easy to clean, but soft enough to give rather than blistering off if it is scraped by an errant anchor.
Today I noticed something... There is no real reason why the lazarette needs a division athwartship. I'm considering a sail locker on each side, by extending my plywood cockpit sides, aft to the transom. I was going to do knees/little stringers that tied into it anyhow... but I've got visions of a v-berth with no sails on it. Of course, this means dragging a sail bag from the cockpit forward... which is all I've really done on Pylasteki, as my shoulders wedge in the forward hatch. Paceship 23 was a different story...
After paint removal, idea stewing, and a little vacuuming I started back my grinding in preparation for glassing inside "The Hole." I discovered today that my bridgedeck is cored, always thought it was solid... saw a light spot in the laminate and thought it was a void... balsa!
My arms are sore from grinding overhead. Ouch.
Zach
Mid-afternoon I took off, and snagged my mast from the boat yard. Brought it back to the shop, and my friend Brian and I stripped the hardware off the lower foot or so. Then he made a set of doublers, 3 and something inches in diameter to weld around an aluminum compression tube. While he did that I bored the holes in my massive pieces of aluminum angle, to take the 1 inch 316 stainless bolt... With that done, we found the center on each side of the extrusion (Thankfully mine has a flat spot where the main sail track goes...) and bored he bored the holes. My mast is slap full of foam.
Anyone have ideas on fishing a new masthead wire in to a solid block of foam?
Anyway, after that I took a huge hose clamp and wrapped it around the mast... marked it with a sharpie... and I cut off the lower few inches that held the end plate that indexes into the mast step firmly in place. 48 years of stainless screws through aluminum into cast aluminum... ain't coming out. I'll have to fish mouth the end of the mast anyway, so that it will clear the deck as it swings its arc. Yes, this is one of those moments in time where one things to themselves... no do-overs!
With that done, it was 4:00... quitting time at the yard, so I took off to the other where Pylasteki resides.
I've decided to do all I can think of inside the cockpit lockers before buttoning them up, today that meant wire brushing the paint off the starboard locker. Whatever it was Pearson used, was some rediculously good paint to still be around 48 years later... at least on my boat it has a pretty tenacious hold, to bad it is hideous speckled stuff in an off-beige brown. I'm going back with a semi-gloss white acrylic enamel (Rustoleum... grin) as I want something smooth enough to be easy to clean, but soft enough to give rather than blistering off if it is scraped by an errant anchor.
Today I noticed something... There is no real reason why the lazarette needs a division athwartship. I'm considering a sail locker on each side, by extending my plywood cockpit sides, aft to the transom. I was going to do knees/little stringers that tied into it anyhow... but I've got visions of a v-berth with no sails on it. Of course, this means dragging a sail bag from the cockpit forward... which is all I've really done on Pylasteki, as my shoulders wedge in the forward hatch. Paceship 23 was a different story...
After paint removal, idea stewing, and a little vacuuming I started back my grinding in preparation for glassing inside "The Hole." I discovered today that my bridgedeck is cored, always thought it was solid... saw a light spot in the laminate and thought it was a void... balsa!
My arms are sore from grinding overhead. Ouch.
Zach
1961 Pearson Triton
http://pylasteki.blogspot.com/
1942 Coast Guard Cutter - Rebuild
http://83footernoel.blogspot.com/
http://pylasteki.blogspot.com/
1942 Coast Guard Cutter - Rebuild
http://83footernoel.blogspot.com/
-
- Candidate for Boat-Obsession Medal
- Posts: 320
- Joined: Thu Aug 16, 2007 6:54 pm
- Boat Name: Lady Kay IV
- Boat Type: 1990 Dragonfly 25
- Location: Bethlehem, PA
- Contact:
Re: The Great Grinder War of 2009
So, let me get this straight.....ripping ONE boat apart is not challenging enough? Got to rip apart another one at the same time? 

Out there, alone, there is only truth.
-
- Boat Obsession Medal Finalist
- Posts: 684
- Joined: Wed Jan 25, 2006 6:28 pm
- Location: Beaufort, North Carolina
- Contact:
Re: The Great Grinder War of 2009





One pays the bills for the other... grin.
Yesterday...
Brian welded up the compression tube and doublers, and filled some of the holes where stuff used to bolt.
While he was running the Tig, I spent some time going over the "list" making sure that all the measurements needed were taken. After the welding was done, I scribed the arc the mast goes through by turning the plate from side to side riding a pencil on the mast. Then transferring the line a 1/2 inch further up... Picked up a plasma cutter, and gave it a try... then backed slowly away and grabbed my trusty jigsaw. Grin. I'm not that artful with something that cuts as fast as plasma...
While I was finishing up fish mouthing the tube... (see picture) he made a new set of jumper strut adjusters. The old ones were crusty aluminum and eaten away... new ones are pieces of stainless allthread.
Finished up around noon, loaded it back up on the truck (tire on the roof of the truck, tire on the back of a trailer... me in the back of the truck picking it up and walking side to side for tight corners.
I bought a bolt with a real wide shoulder, as I'm not sure if this will be my last mast on Pylasteki. I'm going to make a set of plates to carry the boom vang, so when I want to drop the mast everything will rotate around the same pivot point.
Then it was time to get started doing some glass work... except I reached exhaustion, mainly heat... 93 degrees and 80% humidity, all I wanted to do was sleep. Tried to work through it, but no dice... about all I finished was hot coating the plywood panels going into the cockpit. After that I ran over to West Marine to run some pricing on the random tidbits... in airconditioning!
When it cooled off, I went back to... sanding bottom paint. Unfit for anything but the mindless monotony, of waking up to discover that piece of sandpaper had died a long slow death and quit sanding 5 minutes ago...
Question: Black line on mast for boom height = 37 inches off deck?
1961 Pearson Triton
http://pylasteki.blogspot.com/
1942 Coast Guard Cutter - Rebuild
http://83footernoel.blogspot.com/
http://pylasteki.blogspot.com/
1942 Coast Guard Cutter - Rebuild
http://83footernoel.blogspot.com/
- Tim
- Shipwright Extraordinaire
- Posts: 5708
- Joined: Tue Apr 01, 2003 6:39 pm
- Boat Name: Glissando
- Boat Type: Pearson Triton
- Location: Whitefield, ME
- Contact:
Re: The Great Grinder War of 2009
Yup. 37" from the base of the extrusion (i.e. top of the original mast step)Zach wrote:Question: Black line on mast for boom height = 37 inches off deck?
---------------------------------------------------
Forum Founder--No Longer Participating
Forum Founder--No Longer Participating
-
- Candidate for Boat-Obsession Medal
- Posts: 320
- Joined: Thu Aug 16, 2007 6:54 pm
- Boat Name: Lady Kay IV
- Boat Type: 1990 Dragonfly 25
- Location: Bethlehem, PA
- Contact:
Re: The Great Grinder War of 2009
Like that mast foot. Proper overkill. 

Out there, alone, there is only truth.
-
- Boat Obsession Medal Finalist
- Posts: 684
- Joined: Wed Jan 25, 2006 6:28 pm
- Location: Beaufort, North Carolina
- Contact:
Re: The Great Grinder War of 2009
Yesterday I pulled out the masthead sheave, and main halyard.
Todays update involves mainly questions and not much work. Grin.
Pylasteki had a wire to rope spliced halyard, but the rope part has chafed through the outer cover in a few places as she's rigged with all external halyards. I think the big hunk of foam inside the mast negates running internal!
I'm in Greensboro for the weekend to turn a new sheave out of aluminum, old one was phenolic... 6 inch diameter. I've got a 7 inch opening for the sheave box, thinking I may widen it out a bit for a larger diameter so the halyard doesn't rub the mast... got a groooove from the wire. Bummer.
I'm thinking to go with 10mm Staset X halyards, thoughts on diameter? The rope part of mine measures .400, 10mm is .393. May build the new sheave to accomodate a 12mm just in the event of needing to jury rig, it'd take whatever half inch line is handy.
Speaking of jury rigs... anyone have a Triton mast that has a double sheave? I spent some time looking at the mast head, I'd like to have a spare halyard for the main, but it looks a bit thin up there. Thinking I may put a real nice block up for the topping lift, and have a spare halyard ready to go in a locker... pull the topping lift string out, and run the spare up.
My spinnaker halyard is attached to a padeye on the front of the mast that is cast aluminum, someone used a bronze shackle so its eaten away a bit... who do you guys like for mast hardware? Will have some work to do on the other halyards and spinnaker pole storage.
More later...
Zach
Todays update involves mainly questions and not much work. Grin.
Pylasteki had a wire to rope spliced halyard, but the rope part has chafed through the outer cover in a few places as she's rigged with all external halyards. I think the big hunk of foam inside the mast negates running internal!
I'm in Greensboro for the weekend to turn a new sheave out of aluminum, old one was phenolic... 6 inch diameter. I've got a 7 inch opening for the sheave box, thinking I may widen it out a bit for a larger diameter so the halyard doesn't rub the mast... got a groooove from the wire. Bummer.
I'm thinking to go with 10mm Staset X halyards, thoughts on diameter? The rope part of mine measures .400, 10mm is .393. May build the new sheave to accomodate a 12mm just in the event of needing to jury rig, it'd take whatever half inch line is handy.
Speaking of jury rigs... anyone have a Triton mast that has a double sheave? I spent some time looking at the mast head, I'd like to have a spare halyard for the main, but it looks a bit thin up there. Thinking I may put a real nice block up for the topping lift, and have a spare halyard ready to go in a locker... pull the topping lift string out, and run the spare up.
My spinnaker halyard is attached to a padeye on the front of the mast that is cast aluminum, someone used a bronze shackle so its eaten away a bit... who do you guys like for mast hardware? Will have some work to do on the other halyards and spinnaker pole storage.
More later...
Zach
1961 Pearson Triton
http://pylasteki.blogspot.com/
1942 Coast Guard Cutter - Rebuild
http://83footernoel.blogspot.com/
http://pylasteki.blogspot.com/
1942 Coast Guard Cutter - Rebuild
http://83footernoel.blogspot.com/
-
- Deck Grunge Scrubber
- Posts: 39
- Joined: Fri Jun 12, 2009 7:06 am
- Boat Name: Don't Wake Me / Shaken Knot St
- Boat Type: Chrysler C-22 &C-26
Re: The Great Grinder War of 2009
Hey Zach Where is all this going on? I'm just 20 min east of Greensboro and wouldn't mind being a grunt for the experiance. Not a great weekend here to work on my boat due to all the rain, thou I did get a few things done.
Give a howler if you need a extra set of hands, My restoration shop keeps me very busy but also being the boss lets me take time off for things like that.
Give a howler if you need a extra set of hands, My restoration shop keeps me very busy but also being the boss lets me take time off for things like that.
-
- Rough Carpentry Apprentice
- Posts: 52
- Joined: Sun Oct 29, 2006 8:38 am
- Boat Name: Moonshadow
- Boat Type: Seafarer 31 yawl
- Location: Lloyd, Florida
Re: The Great Grinder War of 2009
Zach,
If you are into eye splices, ( I am ) you might stand forwarned that Sayset X is a bear to work with. There must be some sort of enabling trick, but getting the fid through the line was nearly impossible because there is so little give to the weave.
Chris Miller
3 years on the hard Seafarer 31 yawl waiting for the weather to dry out so I can spray paint.
If you are into eye splices, ( I am ) you might stand forwarned that Sayset X is a bear to work with. There must be some sort of enabling trick, but getting the fid through the line was nearly impossible because there is so little give to the weave.
Chris Miller
3 years on the hard Seafarer 31 yawl waiting for the weather to dry out so I can spray paint.
-
- Boat Obsession Medal Finalist
- Posts: 684
- Joined: Wed Jan 25, 2006 6:28 pm
- Location: Beaufort, North Carolina
- Contact:
Re: The Great Grinder War of 2009
Mario: My dad has a shop in Greensboro. Couldn't source materials for this weekend. Pylasteki's rebuild is going on in Beaufort.
Chris: Sounds like fair warning! I'm actually thinking I'll whip the ends and use a bowline for the shackle so I can end for end it, and leave a few extra feet to move the wear spots around... though it is on my list of things to tame, I haven't tried splicing double braid.
Ordered 2 inch by 14 inch x .250 silicon bronze bar stock... 10 pieces. Couple spares, deciding if I want split back stays... Pulled the trigger on 41 bucks each, had another quote come back later today at 30 each. Doh.
Ordered a piece of 3/4 inch phenolic 14 x 23 inches... gonna make a new sheave and spare...
Priced out a sheets of 1/2 inch acrylic, 1/2 inch polycarbonate... xr10 and mr10... (Ouchie on the last one.) Probably going to do 1/2 inch polycarbonate with a UV package, and a sheet of 1/8th inch acrylic in front of it as a sacrificial scratch shield/uv filter.
Went to woodcraft... picked up some goodies I've been lusting over. Mmmm. Ouchie.
Zach
Chris: Sounds like fair warning! I'm actually thinking I'll whip the ends and use a bowline for the shackle so I can end for end it, and leave a few extra feet to move the wear spots around... though it is on my list of things to tame, I haven't tried splicing double braid.
Ordered 2 inch by 14 inch x .250 silicon bronze bar stock... 10 pieces. Couple spares, deciding if I want split back stays... Pulled the trigger on 41 bucks each, had another quote come back later today at 30 each. Doh.
Ordered a piece of 3/4 inch phenolic 14 x 23 inches... gonna make a new sheave and spare...
Priced out a sheets of 1/2 inch acrylic, 1/2 inch polycarbonate... xr10 and mr10... (Ouchie on the last one.) Probably going to do 1/2 inch polycarbonate with a UV package, and a sheet of 1/8th inch acrylic in front of it as a sacrificial scratch shield/uv filter.
Went to woodcraft... picked up some goodies I've been lusting over. Mmmm. Ouchie.
Zach
Last edited by Zach on Mon Aug 03, 2009 7:07 pm, edited 1 time in total.
1961 Pearson Triton
http://pylasteki.blogspot.com/
1942 Coast Guard Cutter - Rebuild
http://83footernoel.blogspot.com/
http://pylasteki.blogspot.com/
1942 Coast Guard Cutter - Rebuild
http://83footernoel.blogspot.com/
-
- Boat Obsession Medal Finalist
- Posts: 684
- Joined: Wed Jan 25, 2006 6:28 pm
- Location: Beaufort, North Carolina
- Contact:
Re: The Great Grinder War of 2009
Question:
Could someone with a Triton that has the original bronze deadlights measure the length and width? I don't particularly need the curve, though it'd help. Trying to figure how many I can get out of a 4x8 sheet, or what size remnants to try and track down. Neglected to think about doing a paint job on the deck while she is out... may as well keep on trucking.
Zach
Could someone with a Triton that has the original bronze deadlights measure the length and width? I don't particularly need the curve, though it'd help. Trying to figure how many I can get out of a 4x8 sheet, or what size remnants to try and track down. Neglected to think about doing a paint job on the deck while she is out... may as well keep on trucking.
Zach
1961 Pearson Triton
http://pylasteki.blogspot.com/
1942 Coast Guard Cutter - Rebuild
http://83footernoel.blogspot.com/
http://pylasteki.blogspot.com/
1942 Coast Guard Cutter - Rebuild
http://83footernoel.blogspot.com/
-
- Boat Obsession Medal Finalist
- Posts: 684
- Joined: Wed Jan 25, 2006 6:28 pm
- Location: Beaufort, North Carolina
- Contact:
Re: The Great Grinder War of 2009
Week ending... Sunday. Grin.
Pylasteki is still out of the water.
Yesterday I leveled her side to side, as I'm contemplating redoing the cockpit like she was a wood...errr composite boat. With her level I can drop a plumb bob and see how far off plumb the cockpit sides would be if I glass them in laying up against the existing cockpit. I don't see much of a reason to have the plywood there, and not use it as a semi-structural member... or at least glass it in and ditch the 1/4 inch thick layer of mat that is the existing cockpit.
Red food coloring looks a lot like blood... I used 3/4 inch clear vinyl, fished it through my lifeline stantion bases on each side and went off the bottom of the boot stripe... which measures perfect each side to the scribed line... on the bottom. Top, eh not so much. Level side to side is all that is going to happen, unless I get the boatyard to pick her back up and re-block her... right now she's bow down so the shear is flat to the horizon... picked her up with the straps a little long, so she's also low to the ground. Sanding bottom paint = ouch.
I've been mulling it over, I think I'm going to paint her topsides and deck while she is out. I'm thinking to roll and tip the deck, for the experience... and spray the hull. Unless anyones rolled, and tipped a hull... maybe the first coat. I brought down my hvlp cup gun... Figuring Alwgrip in Vivid red on the hull, and either Matterhorn or Oyster white on the deck. I've got some scuba tanks, figuring I'll take a regulator and plumb it a long air hose to 1st stage... and see about renting a full face diving helmet. Grin. Either that, or just use a plain old regulator mouthpiece and duct tape the hose to me... bigger grin.
I bought a bunch of 2x10's for staging, and two perfectly straight 2x6's for use as end planes... I want to try out the Tim Lackey Method (TM? ... Grin.) of boot stripe striping, strings and paint cans!
Pretty much though, I've just been sanding bottom paint when ever I have time. I snagged a Porter Cable 7335 (Technically with the dust picker-upper... but haven't tried it, bought a pad so I can use PSA discs) for sanding through the purple shi... stuff, that is between layers of bottom paint. I discovered that a random orbit at 40 grit doesn't melt the purple stuff... but drags down my little finish sander. I'm digging the 7335, just not the most ergonomic thing to grab hold of... gotta talk to PC about making things shaped more like jelly beans.
Oh... my leftover pot of epoxy from my scrap beam kicked off last week to rock candy. So... I did what any sane and logical person would do... I parked my truck on top of it.

I've been running the numbers on the righting moment of tritons... working over the rigging loads. I pulled from the line plans that GZ 30 degrees is 1.3 feet from CG. 1.3 x 7000 = rigging load on empty triton. 1.3 x 10000 = rigging load on loaded Triton. Doing some thinking over 3/16ths or 1/4 inch... breaking strength is just a huge jump between the two. Looks like 16 pounds of wire at 3/16th and 25 at 1/4. Hmmm.... Have to balance overkill with weight weenie. I'm thinking either way, I'll design my chainplates for a 1/2 inch hole and use a 1/2 inch jaw 3/8ths threaded turnbuckle thingamajig (name eludes me at the moment) if I go for 3/16ths. If I go to 1/4 I have to make new tangs for the mast and enlarge the slot on the end of the spreaders not a huge hurdle for me, but just another thing.
I've been having a heck of a time finding load ratings on toggles. ARCO brand looks to be the most massive, may have to call them and ask. i had a chance to fondle some Suncor/Bluewave Quick Attach fittings, swageless mechanical terminals for standing rigging. Look pretty slick, slip the wire in and the jaws on the exterior grab the wire... so no cones, and nothing to replace when re-rigging. I can dig it...
Going for a split backstay, with the split approximately the right height to attach the backstay to the boom while lowering the rig... meaning it won't be flopping around, and I can keep the main halyard rigged to the sail. Oh, and my topping lift wouldn't have to be massive (weight with 1/4 inch wire...) to do the job.
Zach - Visions of flipping the mast down at stubborn bridge tenders whilst flying the bird run through my mind... )
Pylasteki is still out of the water.
Yesterday I leveled her side to side, as I'm contemplating redoing the cockpit like she was a wood...errr composite boat. With her level I can drop a plumb bob and see how far off plumb the cockpit sides would be if I glass them in laying up against the existing cockpit. I don't see much of a reason to have the plywood there, and not use it as a semi-structural member... or at least glass it in and ditch the 1/4 inch thick layer of mat that is the existing cockpit.
Red food coloring looks a lot like blood... I used 3/4 inch clear vinyl, fished it through my lifeline stantion bases on each side and went off the bottom of the boot stripe... which measures perfect each side to the scribed line... on the bottom. Top, eh not so much. Level side to side is all that is going to happen, unless I get the boatyard to pick her back up and re-block her... right now she's bow down so the shear is flat to the horizon... picked her up with the straps a little long, so she's also low to the ground. Sanding bottom paint = ouch.
I've been mulling it over, I think I'm going to paint her topsides and deck while she is out. I'm thinking to roll and tip the deck, for the experience... and spray the hull. Unless anyones rolled, and tipped a hull... maybe the first coat. I brought down my hvlp cup gun... Figuring Alwgrip in Vivid red on the hull, and either Matterhorn or Oyster white on the deck. I've got some scuba tanks, figuring I'll take a regulator and plumb it a long air hose to 1st stage... and see about renting a full face diving helmet. Grin. Either that, or just use a plain old regulator mouthpiece and duct tape the hose to me... bigger grin.
I bought a bunch of 2x10's for staging, and two perfectly straight 2x6's for use as end planes... I want to try out the Tim Lackey Method (TM? ... Grin.) of boot stripe striping, strings and paint cans!
Pretty much though, I've just been sanding bottom paint when ever I have time. I snagged a Porter Cable 7335 (Technically with the dust picker-upper... but haven't tried it, bought a pad so I can use PSA discs) for sanding through the purple shi... stuff, that is between layers of bottom paint. I discovered that a random orbit at 40 grit doesn't melt the purple stuff... but drags down my little finish sander. I'm digging the 7335, just not the most ergonomic thing to grab hold of... gotta talk to PC about making things shaped more like jelly beans.
Oh... my leftover pot of epoxy from my scrap beam kicked off last week to rock candy. So... I did what any sane and logical person would do... I parked my truck on top of it.

I've been running the numbers on the righting moment of tritons... working over the rigging loads. I pulled from the line plans that GZ 30 degrees is 1.3 feet from CG. 1.3 x 7000 = rigging load on empty triton. 1.3 x 10000 = rigging load on loaded Triton. Doing some thinking over 3/16ths or 1/4 inch... breaking strength is just a huge jump between the two. Looks like 16 pounds of wire at 3/16th and 25 at 1/4. Hmmm.... Have to balance overkill with weight weenie. I'm thinking either way, I'll design my chainplates for a 1/2 inch hole and use a 1/2 inch jaw 3/8ths threaded turnbuckle thingamajig (name eludes me at the moment) if I go for 3/16ths. If I go to 1/4 I have to make new tangs for the mast and enlarge the slot on the end of the spreaders not a huge hurdle for me, but just another thing.
I've been having a heck of a time finding load ratings on toggles. ARCO brand looks to be the most massive, may have to call them and ask. i had a chance to fondle some Suncor/Bluewave Quick Attach fittings, swageless mechanical terminals for standing rigging. Look pretty slick, slip the wire in and the jaws on the exterior grab the wire... so no cones, and nothing to replace when re-rigging. I can dig it...
Going for a split backstay, with the split approximately the right height to attach the backstay to the boom while lowering the rig... meaning it won't be flopping around, and I can keep the main halyard rigged to the sail. Oh, and my topping lift wouldn't have to be massive (weight with 1/4 inch wire...) to do the job.
Zach - Visions of flipping the mast down at stubborn bridge tenders whilst flying the bird run through my mind... )
1961 Pearson Triton
http://pylasteki.blogspot.com/
1942 Coast Guard Cutter - Rebuild
http://83footernoel.blogspot.com/
http://pylasteki.blogspot.com/
1942 Coast Guard Cutter - Rebuild
http://83footernoel.blogspot.com/
-
- Master of the Arcane
- Posts: 2272
- Joined: Sat Oct 04, 2003 10:55 pm
- Boat Name: Jenny
- Boat Type: 1966 Pearson Triton
- Location: Rowley, MA
- Contact:
Re: The Great Grinder War of 2009
I really hope you are kidding.I've got some scuba tanks, figuring I'll take a regulator and plumb it a long air hose to 1st stage... and see about renting a full face diving helmet. Grin. Either that, or just use a plain old regulator mouthpiece and duct tape the hose to me... bigger grin.
Why?Going for a split backstay,
-
- Boat Obsession Medal Finalist
- Posts: 684
- Joined: Wed Jan 25, 2006 6:28 pm
- Location: Beaufort, North Carolina
- Contact:
Re: The Great Grinder War of 2009
Not double back stays, but a split one.
The split will be at boom height.
Pull the pin, or maybe pelican hook like on a solent stay...
Connect back stay to the boom.
Now the main sheet is all you need to lower the rig.
One of the pains in the butt about mast lowering is coiling up/getting the back stay out of the way while lowering the mast... tape it to the shrouds? Coil it up on the boom?
I'll be spending the time to make the shrouds have a natural hinge at the same point as the mast tabernacle, so they can stay adjusted (I hope) to hold the mast in column while lowering. I envision a gybe preventer hooked to the boom and the boom set off center a touch on the traveller track to keep it tamed.
My last boat (Paceship 23) had a split backstay, and negated the need for a pushpit by threading the lifeline around rings, with a pelican hook slap in the middle so you both sides dropped limp. I always thought it was a pretty slick setup. Having a wire to lean against while pulling the engine off the mount for support... but without having to lift it over the pushpit rail. Not as big a deal if it were a 2 stroke, but the 4 stroke is heavy... grin.
I wasn't kidding about spraying the boat, as spraying awlgrip is something I want to learn how to do.
I will be building a hookah, as it's called in dive shops for swapping zincs on Noel without having to have my tanks in the water with me... I'm a certified diver anyway. Absolutely no reason why it wouldn't work, unless your jaw muscle gives up half way through a coat... grin. I have however, changed my mind about spraying... as it'd be quite a bit more expensive in materials as vivid red is 330 bucks a gallon, rolling and tipping goes twice as far as sprayed. Looks like around 90 square feet per side to do. 2 coats minimum, 3 preferred...
So... my evil plan of being known as "the guy that sprayed his boat in scuba gear" will have to wait for another day. Grin. Sometimes I think the hard way of doing things has an entertainment value that attracts me as a challenge more than anything else...
This afternoon and evening involved sanding more bottom paint, pricing materials... and trying to get my head back in the game of balancing Noel and Pylasteki at the same time.
Zach
The split will be at boom height.
Pull the pin, or maybe pelican hook like on a solent stay...
Connect back stay to the boom.
Now the main sheet is all you need to lower the rig.
One of the pains in the butt about mast lowering is coiling up/getting the back stay out of the way while lowering the mast... tape it to the shrouds? Coil it up on the boom?
I'll be spending the time to make the shrouds have a natural hinge at the same point as the mast tabernacle, so they can stay adjusted (I hope) to hold the mast in column while lowering. I envision a gybe preventer hooked to the boom and the boom set off center a touch on the traveller track to keep it tamed.
My last boat (Paceship 23) had a split backstay, and negated the need for a pushpit by threading the lifeline around rings, with a pelican hook slap in the middle so you both sides dropped limp. I always thought it was a pretty slick setup. Having a wire to lean against while pulling the engine off the mount for support... but without having to lift it over the pushpit rail. Not as big a deal if it were a 2 stroke, but the 4 stroke is heavy... grin.
I wasn't kidding about spraying the boat, as spraying awlgrip is something I want to learn how to do.
I will be building a hookah, as it's called in dive shops for swapping zincs on Noel without having to have my tanks in the water with me... I'm a certified diver anyway. Absolutely no reason why it wouldn't work, unless your jaw muscle gives up half way through a coat... grin. I have however, changed my mind about spraying... as it'd be quite a bit more expensive in materials as vivid red is 330 bucks a gallon, rolling and tipping goes twice as far as sprayed. Looks like around 90 square feet per side to do. 2 coats minimum, 3 preferred...
So... my evil plan of being known as "the guy that sprayed his boat in scuba gear" will have to wait for another day. Grin. Sometimes I think the hard way of doing things has an entertainment value that attracts me as a challenge more than anything else...
This afternoon and evening involved sanding more bottom paint, pricing materials... and trying to get my head back in the game of balancing Noel and Pylasteki at the same time.
Zach
1961 Pearson Triton
http://pylasteki.blogspot.com/
1942 Coast Guard Cutter - Rebuild
http://83footernoel.blogspot.com/
http://pylasteki.blogspot.com/
1942 Coast Guard Cutter - Rebuild
http://83footernoel.blogspot.com/
-
- Master of the Arcane
- Posts: 2272
- Joined: Sat Oct 04, 2003 10:55 pm
- Boat Name: Jenny
- Boat Type: 1966 Pearson Triton
- Location: Rowley, MA
- Contact:
Re: The Great Grinder War of 2009
I am familiar with SCUBA and Hookah systems. I am also familiar with supplied air respirators. From a safety standpoint there is a world of difference. Keeping the iso-cyanides and other baddies away from your eyes and lips is important. The better sealing of a supplied air system makes it a much safer system. Cleanup might be an issue. I can easily clean or replace at little cost the facesc reen on a supplied air mask. A diving helmet might not be so easy. I am not even sure how the rubber in SCUBA equipment likes the airborne solvents. You might find yourself buying new equipment sooner than you expected. Your spraying environment might be different than the one I experienced. I was inside an enclosed bay and atomized paint hung like a thick cloud in the air. You could smell death. If you are basically outside you might be able to get away with less but I personally, think these materials are not where I would try to save money over my health.
As for costs, I think I paid about the same for my Awlcraft topcoat but the three coats sprayed on only used about a quart. I figure I have a lifetime supply of topcoat waiting for me assuming I repaint every ten years. In any case, by the time you factor in all the other costs in materials and labor, is $300 and change really that big a deal?
Figment has a thread around here from a few years ago that covered his roll and tip the hull experience. I can't remember how much he used but I know it was talked about in that thread.
As for costs, I think I paid about the same for my Awlcraft topcoat but the three coats sprayed on only used about a quart. I figure I have a lifetime supply of topcoat waiting for me assuming I repaint every ten years. In any case, by the time you factor in all the other costs in materials and labor, is $300 and change really that big a deal?
Figment has a thread around here from a few years ago that covered his roll and tip the hull experience. I can't remember how much he used but I know it was talked about in that thread.
I guess I just can't see that being all that much of a pain. But then again I don't duck under many bridges and don't have a rig that is set up to do it. On my original rig, I had a short length of wire connected to the backstay with a nico-press. The wire had a clip on the end and it normally was clipped to the backstay so that the wire laid alongside the backstay. The clip could also be attached to the boom which acted like a fixed topping lift. I never found much use for it and occasionally I would reach for the backstay and grab the nicopress instead (ouch!) so I never really thought about incorporating it into my new backstay.One of the pains in the butt about mast lowering is coiling up/getting the back stay out of the way while lowering the mast.
-
- Damned Because It's All Connected
- Posts: 2847
- Joined: Tue Apr 08, 2003 9:32 am
- Boat Name: Triton
- Boat Type: Grand Banks 42
- Location: L.I. Sound
Re: The Great Grinder War of 2009
Or shackle your spectra core main halyard to the end of the boom and let your backstay be a backstay.Zach wrote:Not double back stays, but a split one.
The split will be at boom height.
Pull the pin, or maybe pelican hook like on a solent stay...
Connect back stay to the boom.
Now the main sheet is all you need to lower the rig.
-
- Damned Because It's All Connected
- Posts: 2847
- Joined: Tue Apr 08, 2003 9:32 am
- Boat Name: Triton
- Boat Type: Grand Banks 42
- Location: L.I. Sound
Re: The Great Grinder War of 2009
I think I used two quarts or so of topcoat, but that's probably because it took me seven coats to get it right.
-
- Boat Obsession Medal Finalist
- Posts: 684
- Joined: Wed Jan 25, 2006 6:28 pm
- Location: Beaufort, North Carolina
- Contact:
Re: The Great Grinder War of 2009
Good information, thanks guys.
Britton, good thought on iso-cyanides and skin along with equipment prices. I've got a line on a military surplus compressor for breathable air for future adventures... $300 bucks in the grand scheme of things isn't a lot, but in the scheme of this rebuild I've done it a few to many times over the last few weeks. MR10 polycarbonate for new deadlights, 655 Silicon bronze chainplates, a day and a half of machine shop/welding hours, all marine grade plywood and west systems epoxy... tools, etc, etc. My cash burn doesn't quite rival GM, but it sure feels like it! I've got to keep enough stashed away to pay the yard bill when she goes back overboard!
Spray environment = travel lift over the top of the boat and tarps around it. I'm used to out doors no shielding required... which is what I was thinking. Spraying isn't an option now for Pylasteki, as the yard just moved a boat into the one location the EPA will allow spray painting, and will not be finished up for a few weeks. I can't swing the yard bills and chance the weather not co-operating waiting a month.
I'm on the hunt for some vivid red as close to cost as I can get it. Good to hear that it covers better than I was thinking. If not red, then I'm thinking Hatteras off-white for hull and deck, with sea foam non-skid. I can buy everything but the red locally. I'm wrestling with red being hotter in the sun too, but I do like red paint is the one thing where function follows form. (Grin)
At the moment, I'm going to hold off on the standing rigging refit, and use mechanical connections on the bottom of the wire I have for the rest of the season and re-assess. The math works out to a 2x safety factory on a 7k lb boat, and a 1.5X on a 10,000 pound. The fact that a whole lot of Tritons have been rigged in 3/16th and the sticks stay up, speaks loud enough even for me. <Gnashes teeth at leaving stuff as designed... grin>
In other news, a Herreshoff from 1904 named Margaret hauled out beside me... First time I've seen one out of the water in person... Humina humina!
Thanks for the thoughts guys, it is appreciated.
Zach
Britton, good thought on iso-cyanides and skin along with equipment prices. I've got a line on a military surplus compressor for breathable air for future adventures... $300 bucks in the grand scheme of things isn't a lot, but in the scheme of this rebuild I've done it a few to many times over the last few weeks. MR10 polycarbonate for new deadlights, 655 Silicon bronze chainplates, a day and a half of machine shop/welding hours, all marine grade plywood and west systems epoxy... tools, etc, etc. My cash burn doesn't quite rival GM, but it sure feels like it! I've got to keep enough stashed away to pay the yard bill when she goes back overboard!
Spray environment = travel lift over the top of the boat and tarps around it. I'm used to out doors no shielding required... which is what I was thinking. Spraying isn't an option now for Pylasteki, as the yard just moved a boat into the one location the EPA will allow spray painting, and will not be finished up for a few weeks. I can't swing the yard bills and chance the weather not co-operating waiting a month.
I'm on the hunt for some vivid red as close to cost as I can get it. Good to hear that it covers better than I was thinking. If not red, then I'm thinking Hatteras off-white for hull and deck, with sea foam non-skid. I can buy everything but the red locally. I'm wrestling with red being hotter in the sun too, but I do like red paint is the one thing where function follows form. (Grin)
At the moment, I'm going to hold off on the standing rigging refit, and use mechanical connections on the bottom of the wire I have for the rest of the season and re-assess. The math works out to a 2x safety factory on a 7k lb boat, and a 1.5X on a 10,000 pound. The fact that a whole lot of Tritons have been rigged in 3/16th and the sticks stay up, speaks loud enough even for me. <Gnashes teeth at leaving stuff as designed... grin>
In other news, a Herreshoff from 1904 named Margaret hauled out beside me... First time I've seen one out of the water in person... Humina humina!
Thanks for the thoughts guys, it is appreciated.
Zach
1961 Pearson Triton
http://pylasteki.blogspot.com/
1942 Coast Guard Cutter - Rebuild
http://83footernoel.blogspot.com/
http://pylasteki.blogspot.com/
1942 Coast Guard Cutter - Rebuild
http://83footernoel.blogspot.com/
-
- Almost a Finish Carpenter
- Posts: 99
- Joined: Tue Sep 23, 2008 11:18 pm
- Boat Name: TBD
- Boat Type: Westsail 32
- Location: Jacksonville, FL
- Contact:
Re: The Great Grinder War of 2009
Hey Zach,
...post a picture of Margaret will ya? I need a new centerfold for the wall!
-Brian
...post a picture of Margaret will ya? I need a new centerfold for the wall!
-Brian
"My best days are ahead of me..."
http://www.seasprite217.blogspot.com
http://www.westsailstory.blogspot.com
http://www.seasprite217.blogspot.com
http://www.westsailstory.blogspot.com
- Tim
- Shipwright Extraordinaire
- Posts: 5708
- Joined: Tue Apr 01, 2003 6:39 pm
- Boat Name: Glissando
- Boat Type: Pearson Triton
- Location: Whitefield, ME
- Contact:
Re: The Great Grinder War of 2009
Hello, Hamilton Marine? I'd like to order two quarts of Alexseal Vivid Red, item # 731362, at your excellent retail price of $77.99 each.Zach wrote:I'm on the hunt for some vivid red as close to cost as I can get it...I can buy everything but the red locally.
Alternatively:
Hello, Jamestown Distributors? I'd like to order two quarts of Awlgrip Vivid Red, item # AWL-G7367Q, at your reasonable-enough price of $93.14 each.
Mail order is really cool, and it takes 4 minutes. ;<)
---------------------------------------------------
Forum Founder--No Longer Participating
Forum Founder--No Longer Participating
-
- Boat Obsession Medal Finalist
- Posts: 684
- Joined: Wed Jan 25, 2006 6:28 pm
- Location: Beaufort, North Carolina
- Contact:
Re: The Great Grinder War of 2009
I can always count on Tim to know where to go to get the goods, the good stuff... Grin.
I'm just a little disillusioned, as I saw the markup go into my price for a gallon... 66% on the calculator at one of the purveyors of fine nautical goodies I frequent... 340 bucks a gallon. Full retail 4 and change. Ouchie mama... means 204 a gallon at their cost.
Me thinks it's about time I become incorporated and set up some wholesale accounts. It's the little stuff that adds up, but higher unit price shock one into awareness.
Anyhow, I'll snap some pictures of Margaret tomorrow. Pylasteki is getting moved, and should offer a pretty slick picture, as she'll sit under the height of Margarets counter!
I removed my pushpit, outboard, outboard bracket. De-lettered, pulled off the stainless trim on the transom... and de-greased. Made a long board that takes two 16 inch pieces of air file paper out of a piece of scrap starboard a friend gave me, cut out some handles on the bandsaw and rounded them over with my router. Countersunk the screws put in one per side so the handles can rotate and turn to whatever position is easiest on the wrists.
Went to town on the transom with 36 grit paper for an hour. Pulled out some 40 grit on the 7335 for a half hour... Decided I'd try a power planer. Neglected to look at the condition of the blades before starting.... derrr. Forgot I banged a nail working on Noels decks a few weeks ago. The gelcoat is chalk. I've got a full coat of white, over a full coat of black as thick as Pearson is known for doing. (almost a 1/4 inch along the stem!) Still in the white gel, I want to take it back as far as I can so whatever cracks don't show through. Plus I figure that much chalk must weigh something.... grin. Running my hands around the hull, my port aft lower chainplate knee is a bump on the outside of the hull. Dusting on some flat black paint on the transom, you can clearly see the back stay chainplate knee outlined. I'm a little amused at the thickness, currently I'm planning to knock it back down, tomorrow I'll grab a worn out flap disc and artfully sculpt it down... don't follow the instructions for polishing stainless, 15-20 degree angle.. lay it flat and use about the same touch as a you'd sculpt styrofoam with a blow torch.... Vertical passes only so no scars running through curves are put in that can't easily be longboarded out...
Fun fun fun! Bottom paint is almost all gone. It really is amazing the difference good sandpaper makes... just have to be on the ball enough to know when its surpassed its useful life!
My wailing about the cost of paint and other goodies requires that I do some talking for my fellow budget minded folks. My polycarbonate came in... in case anyone wants the good stuff, track down a plastics distributor well in advance of when you need the stuff. Put in a request that they keep the remnants of a size slightly larger than what you need rather than making scrap from a full sheet. I go through Piedmont Plastics. 5 pieces of GE MR10 (Structural glazing, the stuff they use on skyscrapers... 10 year UV package, 10 year scratch) in 1/2 inch for 50 bucks a piece. The sheet is almost a thousand bucks retail. Same thing for the Phenolic... bought a hunk of 3/4 14x24 for 50 bucks. Full sheet of that would be 1700 full retail. Helps to scrounge, but you have to know what you want... and how much. Some came from Nashville, one from Sanfrancisco... If you don't care that it'll take two weeks for trucks going from one warehouse to another to play connect the dots, it'll save you a lot of money.
Saw yesterday that my backstay's upper clevis pin is teeny tiny, same size as the 1/4 inch stuff on the jumper stays.
Zach
I'm just a little disillusioned, as I saw the markup go into my price for a gallon... 66% on the calculator at one of the purveyors of fine nautical goodies I frequent... 340 bucks a gallon. Full retail 4 and change. Ouchie mama... means 204 a gallon at their cost.
Me thinks it's about time I become incorporated and set up some wholesale accounts. It's the little stuff that adds up, but higher unit price shock one into awareness.
Anyhow, I'll snap some pictures of Margaret tomorrow. Pylasteki is getting moved, and should offer a pretty slick picture, as she'll sit under the height of Margarets counter!
I removed my pushpit, outboard, outboard bracket. De-lettered, pulled off the stainless trim on the transom... and de-greased. Made a long board that takes two 16 inch pieces of air file paper out of a piece of scrap starboard a friend gave me, cut out some handles on the bandsaw and rounded them over with my router. Countersunk the screws put in one per side so the handles can rotate and turn to whatever position is easiest on the wrists.
Went to town on the transom with 36 grit paper for an hour. Pulled out some 40 grit on the 7335 for a half hour... Decided I'd try a power planer. Neglected to look at the condition of the blades before starting.... derrr. Forgot I banged a nail working on Noels decks a few weeks ago. The gelcoat is chalk. I've got a full coat of white, over a full coat of black as thick as Pearson is known for doing. (almost a 1/4 inch along the stem!) Still in the white gel, I want to take it back as far as I can so whatever cracks don't show through. Plus I figure that much chalk must weigh something.... grin. Running my hands around the hull, my port aft lower chainplate knee is a bump on the outside of the hull. Dusting on some flat black paint on the transom, you can clearly see the back stay chainplate knee outlined. I'm a little amused at the thickness, currently I'm planning to knock it back down, tomorrow I'll grab a worn out flap disc and artfully sculpt it down... don't follow the instructions for polishing stainless, 15-20 degree angle.. lay it flat and use about the same touch as a you'd sculpt styrofoam with a blow torch.... Vertical passes only so no scars running through curves are put in that can't easily be longboarded out...
Fun fun fun! Bottom paint is almost all gone. It really is amazing the difference good sandpaper makes... just have to be on the ball enough to know when its surpassed its useful life!
My wailing about the cost of paint and other goodies requires that I do some talking for my fellow budget minded folks. My polycarbonate came in... in case anyone wants the good stuff, track down a plastics distributor well in advance of when you need the stuff. Put in a request that they keep the remnants of a size slightly larger than what you need rather than making scrap from a full sheet. I go through Piedmont Plastics. 5 pieces of GE MR10 (Structural glazing, the stuff they use on skyscrapers... 10 year UV package, 10 year scratch) in 1/2 inch for 50 bucks a piece. The sheet is almost a thousand bucks retail. Same thing for the Phenolic... bought a hunk of 3/4 14x24 for 50 bucks. Full sheet of that would be 1700 full retail. Helps to scrounge, but you have to know what you want... and how much. Some came from Nashville, one from Sanfrancisco... If you don't care that it'll take two weeks for trucks going from one warehouse to another to play connect the dots, it'll save you a lot of money.
Saw yesterday that my backstay's upper clevis pin is teeny tiny, same size as the 1/4 inch stuff on the jumper stays.
Zach
1961 Pearson Triton
http://pylasteki.blogspot.com/
1942 Coast Guard Cutter - Rebuild
http://83footernoel.blogspot.com/
http://pylasteki.blogspot.com/
1942 Coast Guard Cutter - Rebuild
http://83footernoel.blogspot.com/
-
- Boat Obsession Medal Finalist
- Posts: 684
- Joined: Wed Jan 25, 2006 6:28 pm
- Location: Beaufort, North Carolina
- Contact:
Re: The Great Grinder War of 2009
So... Another week has gone by (for all intents...)
I've pulled off the stainless rubrail, and de-gooped it with a razor blade. I think there is some pre-historic silicone present... so working dillegently to remove all traces before sanding anything. Thats three nights work. The yard moved her out of the way, so I had to jockey my pile of lumber and table, tarp, cockpit parts... etc from one side to the other, and clean up my old spot of spent box fans, grinding discs, and vacuums... grin.
I've been building a staging, stacking up pallets and laying 2x10's across them I think it'll work out nicely. Really wish she was blocked higher for doing bottom work, but kind of nice for setting up staging, I'm 3 high in the bow and two in the back.
Noel has been keeping me busy otherwise... rebuilding the transom, and resheathing 30 feet of plywood and glass... Stepping slowly away from the skill saw... but, rotten wood is my bane... kinda stole priority from Pylasteki.
Margaret.




Zach
I've pulled off the stainless rubrail, and de-gooped it with a razor blade. I think there is some pre-historic silicone present... so working dillegently to remove all traces before sanding anything. Thats three nights work. The yard moved her out of the way, so I had to jockey my pile of lumber and table, tarp, cockpit parts... etc from one side to the other, and clean up my old spot of spent box fans, grinding discs, and vacuums... grin.
I've been building a staging, stacking up pallets and laying 2x10's across them I think it'll work out nicely. Really wish she was blocked higher for doing bottom work, but kind of nice for setting up staging, I'm 3 high in the bow and two in the back.
Noel has been keeping me busy otherwise... rebuilding the transom, and resheathing 30 feet of plywood and glass... Stepping slowly away from the skill saw... but, rotten wood is my bane... kinda stole priority from Pylasteki.
Margaret.




Zach
1961 Pearson Triton
http://pylasteki.blogspot.com/
1942 Coast Guard Cutter - Rebuild
http://83footernoel.blogspot.com/
http://pylasteki.blogspot.com/
1942 Coast Guard Cutter - Rebuild
http://83footernoel.blogspot.com/
Re: The Great Grinder War of 2009
Maybe it's just me, but can you run over and toss a stand under the stern sections of Margaret? Eek, that looks like a lot of boat just itching to droop.
Glad to hear you're still skirmishing :)
Rachel
(Picturing a giant heap of spent box fans, which for some reason is striking me funny. Maybe I've had too much sun.)
Glad to hear you're still skirmishing :)
Rachel
(Picturing a giant heap of spent box fans, which for some reason is striking me funny. Maybe I've had too much sun.)
-
- Boat Obsession Medal Finalist
- Posts: 684
- Joined: Wed Jan 25, 2006 6:28 pm
- Location: Beaufort, North Carolina
- Contact:
Re: The Great Grinder War of 2009
Agreed, but if you look close... the stands can't go high enough to catch the counter!
Margaret is a beauty inside and out... envy!
Anyhow, been doing some more sanding of gelcoat on Pylasteki. Tried doing my norm of running an angle grinder with a flap disc over the surface... but the hull has to many curves leaving about a 3/4 inch stripe working up and down. Perhaps faster than straight sand paper, but takes to much concentration to keep it moving/overlapping what is there.
I need to order some decent sandpaper and get on with the program.
Noel has been keeping me busy the last few weeks. You can now step right off the staging and walk through her transom, and no planks from the waterline up over the 30 feet from the starboard side. Reworking some framing, and deciding whether or not to do a mahogany transom. 13.5 feet wide... I found some of the prettiest cathedral grained boards that are only 6 inches wider than the planer at the yard can handle...
Anyway, gotta get my energy levels and enthusiasm cranked back up. Figuring that'll start once Noel is back on construction rather than destruction... or the "What the heck did I do" stage, as I like to call it...
Zach
Margaret is a beauty inside and out... envy!
Anyhow, been doing some more sanding of gelcoat on Pylasteki. Tried doing my norm of running an angle grinder with a flap disc over the surface... but the hull has to many curves leaving about a 3/4 inch stripe working up and down. Perhaps faster than straight sand paper, but takes to much concentration to keep it moving/overlapping what is there.
I need to order some decent sandpaper and get on with the program.
Noel has been keeping me busy the last few weeks. You can now step right off the staging and walk through her transom, and no planks from the waterline up over the 30 feet from the starboard side. Reworking some framing, and deciding whether or not to do a mahogany transom. 13.5 feet wide... I found some of the prettiest cathedral grained boards that are only 6 inches wider than the planer at the yard can handle...
Anyway, gotta get my energy levels and enthusiasm cranked back up. Figuring that'll start once Noel is back on construction rather than destruction... or the "What the heck did I do" stage, as I like to call it...
Zach
1961 Pearson Triton
http://pylasteki.blogspot.com/
1942 Coast Guard Cutter - Rebuild
http://83footernoel.blogspot.com/
http://pylasteki.blogspot.com/
1942 Coast Guard Cutter - Rebuild
http://83footernoel.blogspot.com/
- Tim
- Shipwright Extraordinaire
- Posts: 5708
- Joined: Tue Apr 01, 2003 6:39 pm
- Boat Name: Glissando
- Boat Type: Pearson Triton
- Location: Whitefield, ME
- Contact:
Re: The Great Grinder War of 2009
Let us know when you get back to work on the real project. (that's the Triton, of course.)
Meanwhile, just order this sandpaper for your 5" right angle random orbit sander (DA). Your grinder belongs nowhere near your topsides. Ever.
Meanwhile, just order this sandpaper for your 5" right angle random orbit sander (DA). Your grinder belongs nowhere near your topsides. Ever.
---------------------------------------------------
Forum Founder--No Longer Participating
Forum Founder--No Longer Participating
-
- Boat Obsession Medal Finalist
- Posts: 684
- Joined: Wed Jan 25, 2006 6:28 pm
- Location: Beaufort, North Carolina
- Contact:
Re: The Great Grinder War of 2009
I know I know... It was one of those "forgive me for I have sinned" moments that what works on a 15 foot radius doesn't work on a 2 foot radius... folks that do small boats for a living are working harder for their dollars!
I've got about 2 feet of gelcoat off the port side now, by golly they sprayed the stuff on thick!
I've got about 2 feet of gelcoat off the port side now, by golly they sprayed the stuff on thick!
1961 Pearson Triton
http://pylasteki.blogspot.com/
1942 Coast Guard Cutter - Rebuild
http://83footernoel.blogspot.com/
http://pylasteki.blogspot.com/
1942 Coast Guard Cutter - Rebuild
http://83footernoel.blogspot.com/
-
- Boat Obsession Medal Finalist
- Posts: 684
- Joined: Wed Jan 25, 2006 6:28 pm
- Location: Beaufort, North Carolina
- Contact:
Re: The Great Grinder War of 2009
That McMaster-Carr sandpaper is some lovely stuff.
Progress report: More sanding done on hull. Port side nearly 23% completion. (% made up, but added for dramatic effect.)
Noel report... Well check here: http://83footernoel.blogspot.com/search ... -results=7
First layer of plywood is on the transom... thinking I may take a break and switch over to "The Glass Boat" and make another thrust in the great grinder war... before it becomes 2010.
Zach
Progress report: More sanding done on hull. Port side nearly 23% completion. (% made up, but added for dramatic effect.)
Noel report... Well check here: http://83footernoel.blogspot.com/search ... -results=7
First layer of plywood is on the transom... thinking I may take a break and switch over to "The Glass Boat" and make another thrust in the great grinder war... before it becomes 2010.
Zach
1961 Pearson Triton
http://pylasteki.blogspot.com/
1942 Coast Guard Cutter - Rebuild
http://83footernoel.blogspot.com/
http://pylasteki.blogspot.com/
1942 Coast Guard Cutter - Rebuild
http://83footernoel.blogspot.com/
Re: The Great Grinder War of 2009
Now that you've discovered the "fun" sandpaper discs, who wants to stop?
Glad to hear the war isn't over :)
Rachel
Glad to hear the war isn't over :)
Rachel